Part 3 of a 3 parts training trip to Japan by Tinctoria, November-December 2023
I had the chance of meeting Hiroaki Kuno a few years ago when he came to train us in shibori-zome over a week-end at Couleur Garance.
As you those who have been following my work would know, I have since then been extensively practising shibori with natural indigo. With ample occasions to realise how hard it is to get even the “simplest” of these techniques right.
Shibori-zome includes an endless variety of reserve technique to produce pattern on fabric when applied before dyeing. Traditional patterns where executed by persons with infinite dexterity and infinite patience. Knot by knot, stitch by stitch, fold by fold, the fabric is crumpled into a much smaller bundle before being immersed in the dye. Once dyed, the fabric is rinsed and the reserve removed to reveal an infinity of patterns.
Photo credit: Nobuki KAWAHARAZAKI
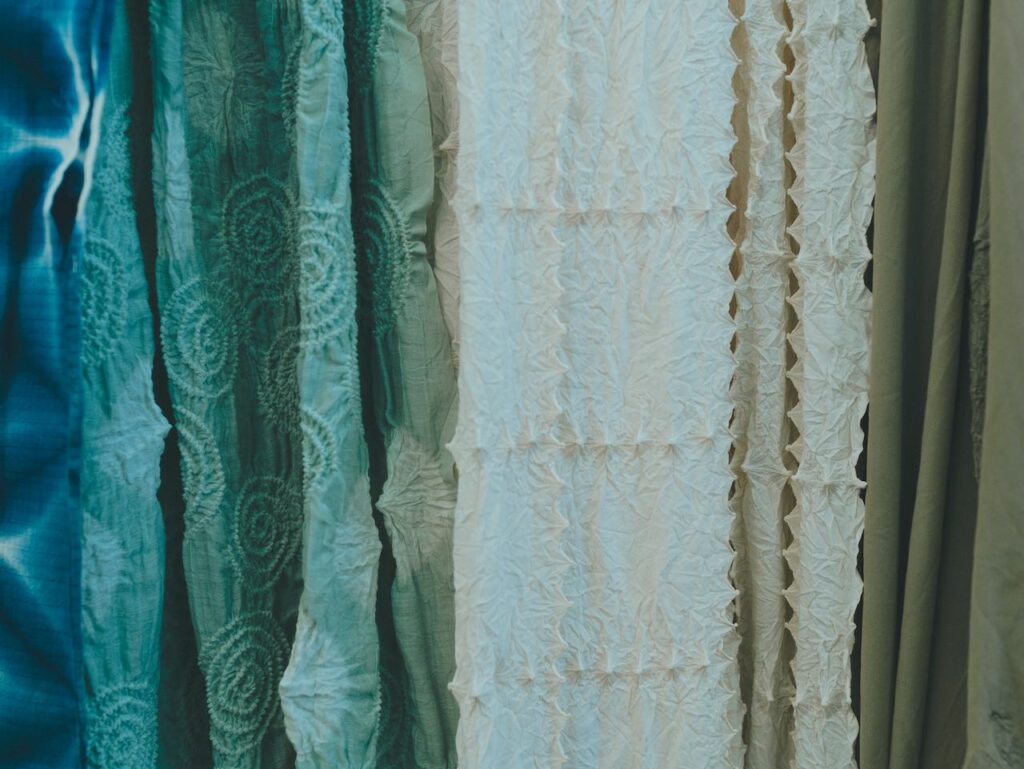
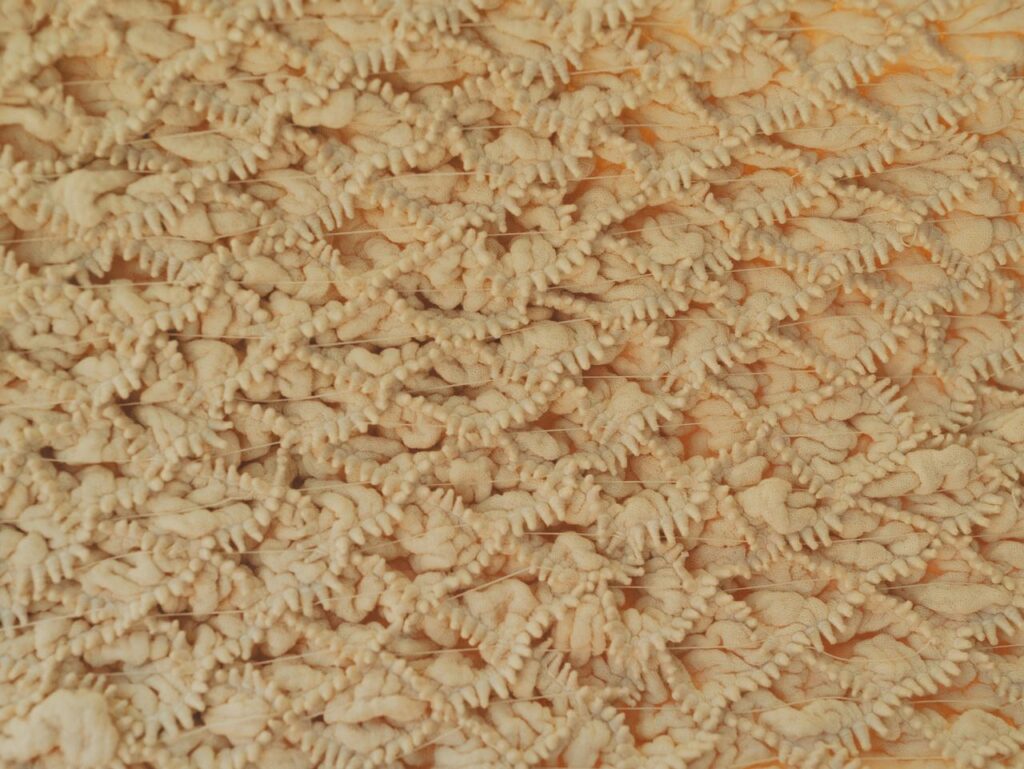
To start, the fabric gets marked, in order for the knots of stitches to be positioned right. The punched sheets of paper are the treasure of each atelier
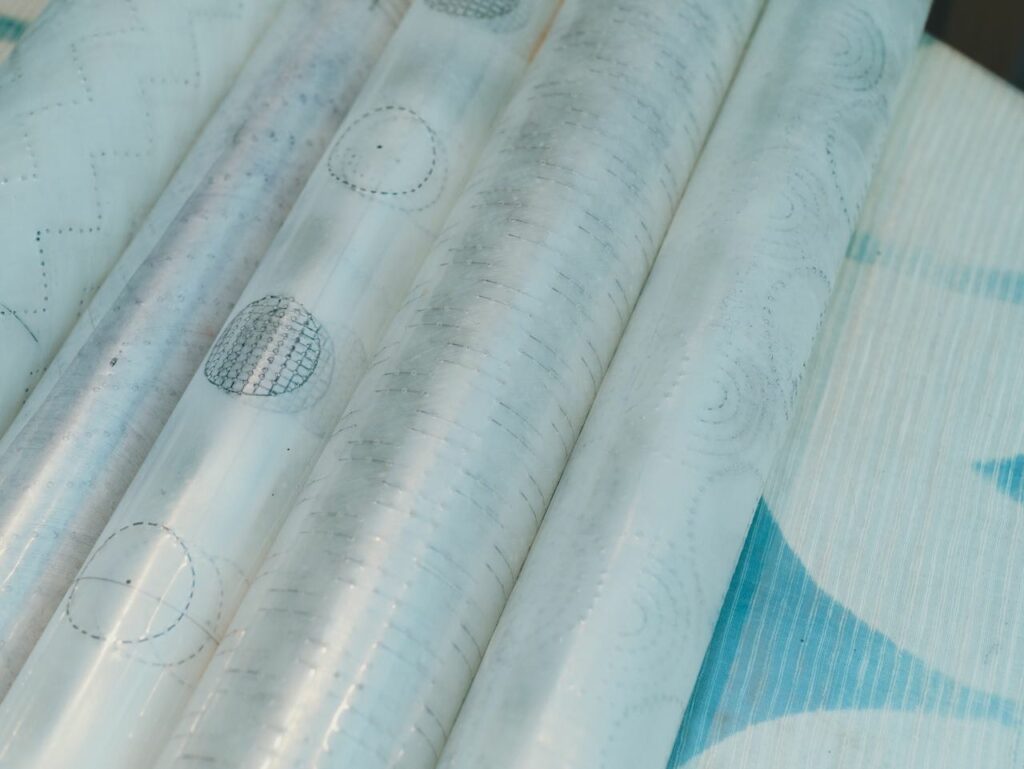
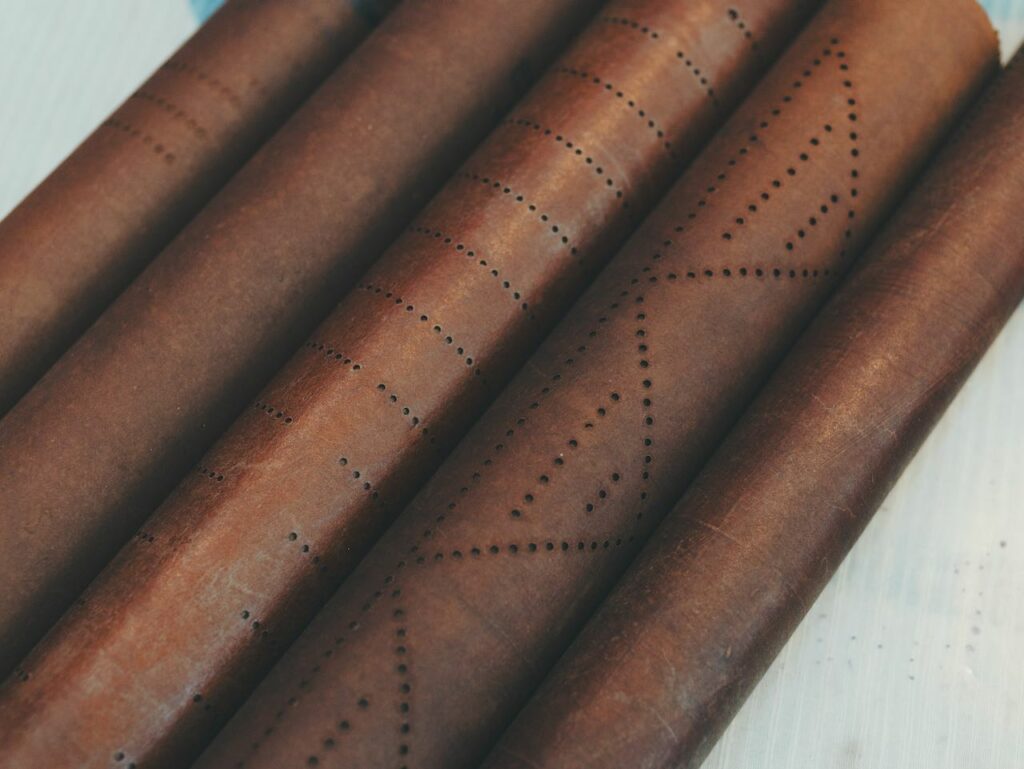
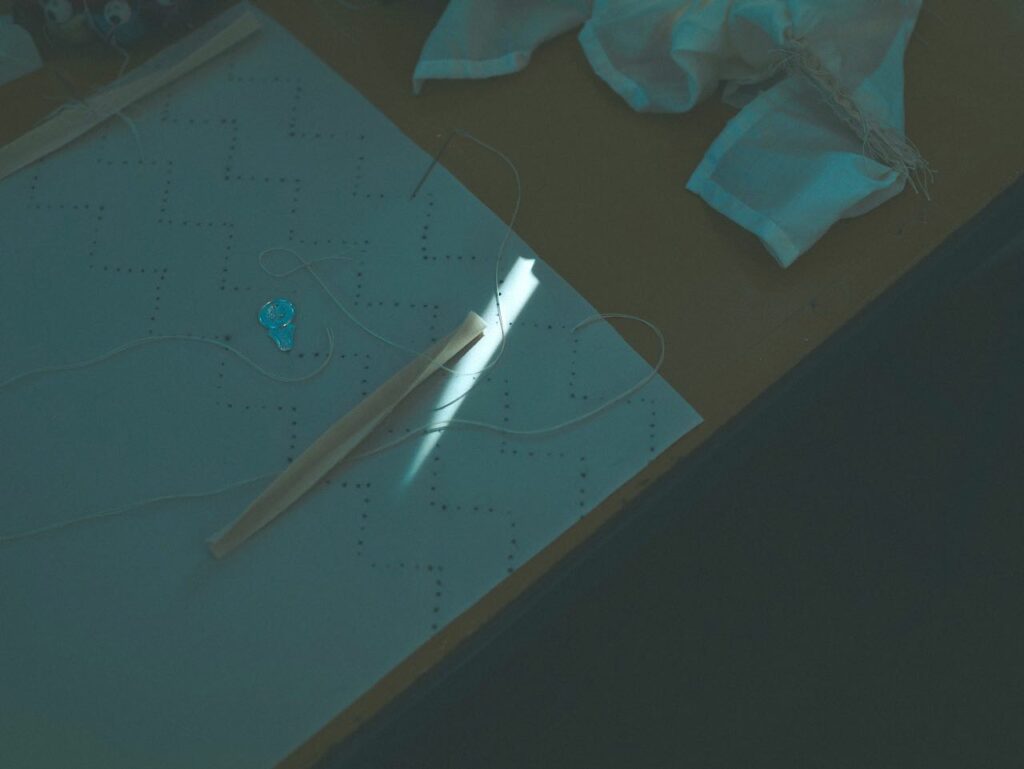
Stitching, folding and / or knowing then starts, and can go on for days and days. In our case, a few hours was all we had so some of it was done overnight at the hotel, in true Japanese style 😉
This was a fabulous opportunity to not just see the technique from the hands of a master, but also to get one’s handicraft corrected and improved. Pure gold.
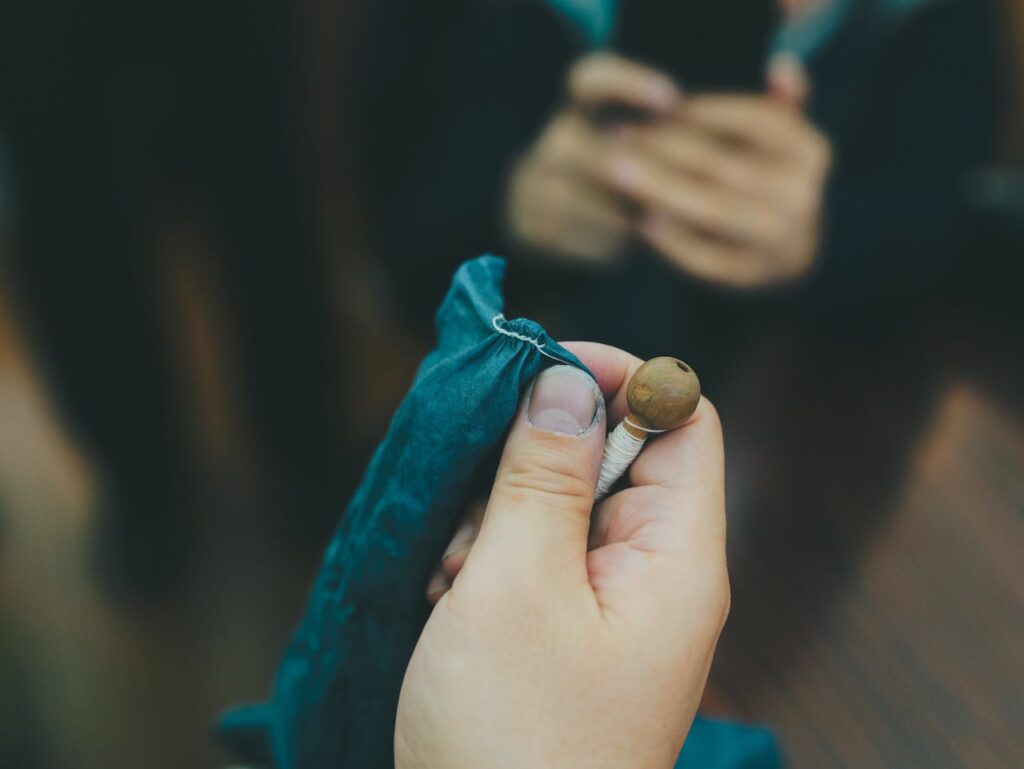
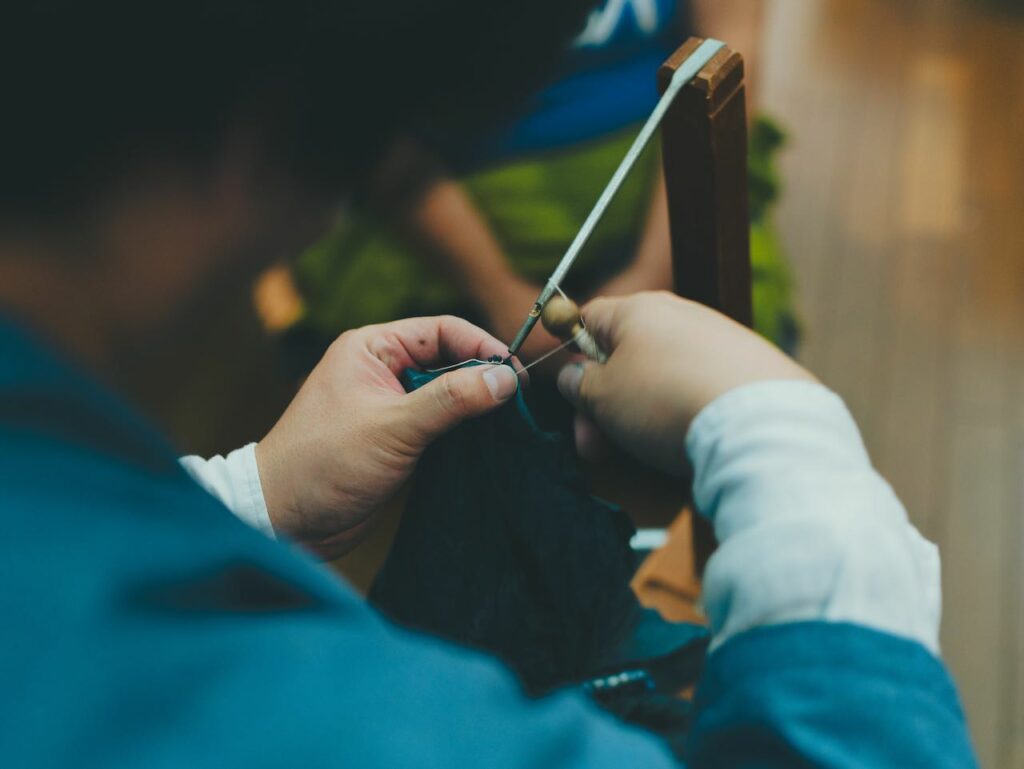
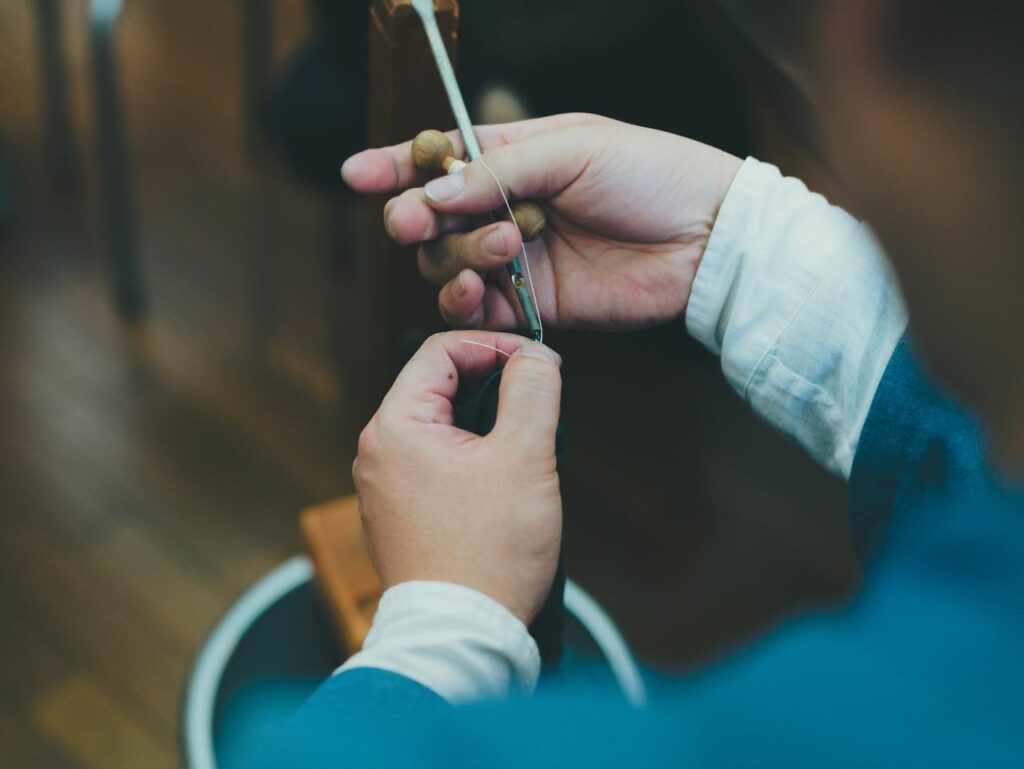
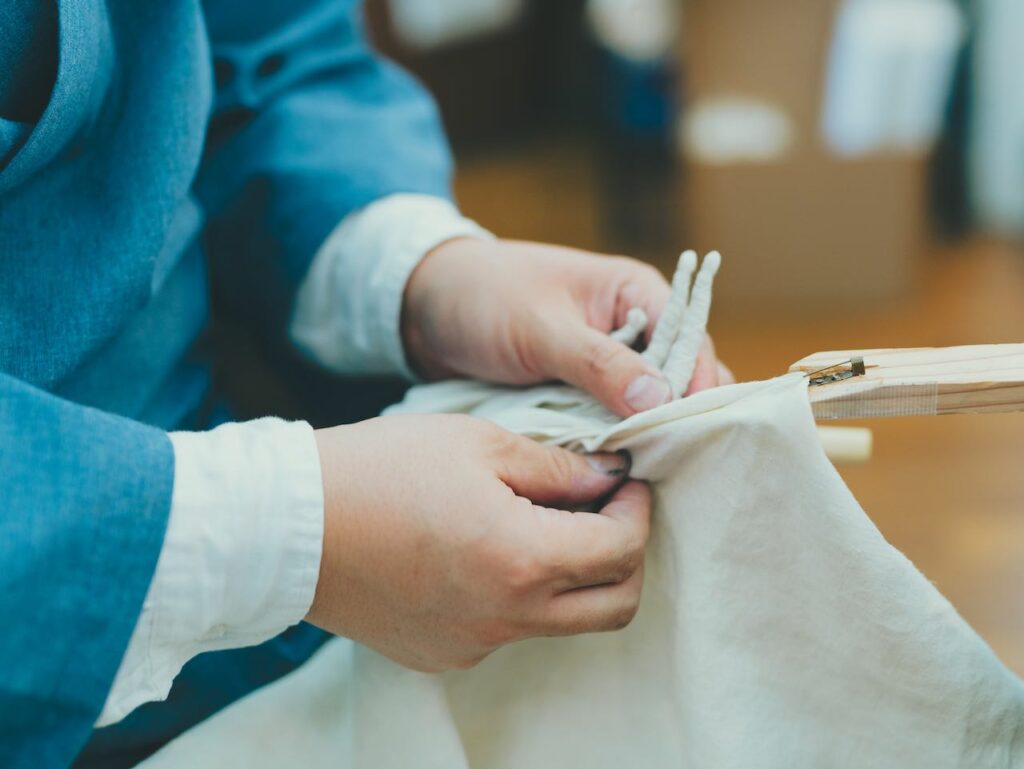
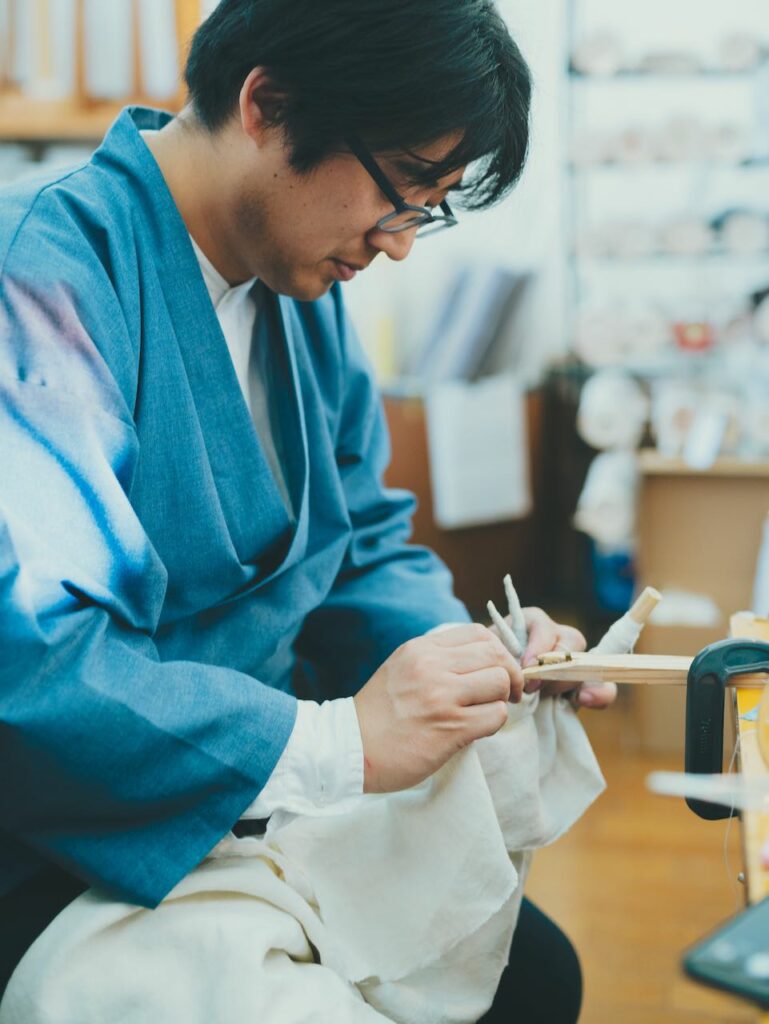
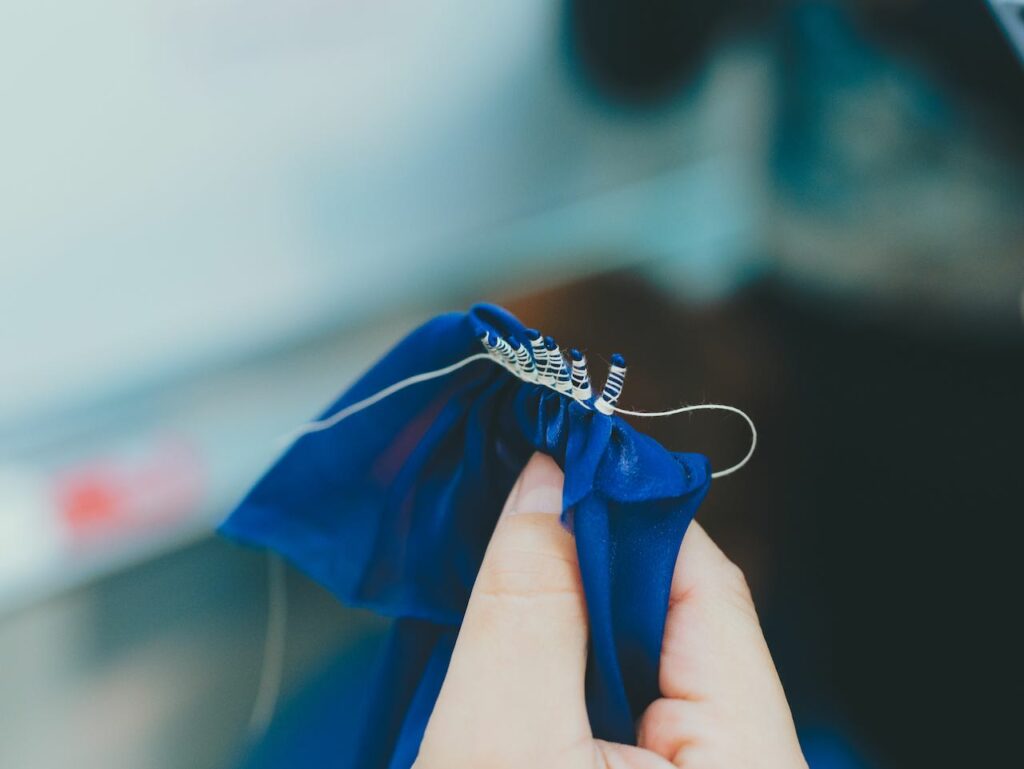
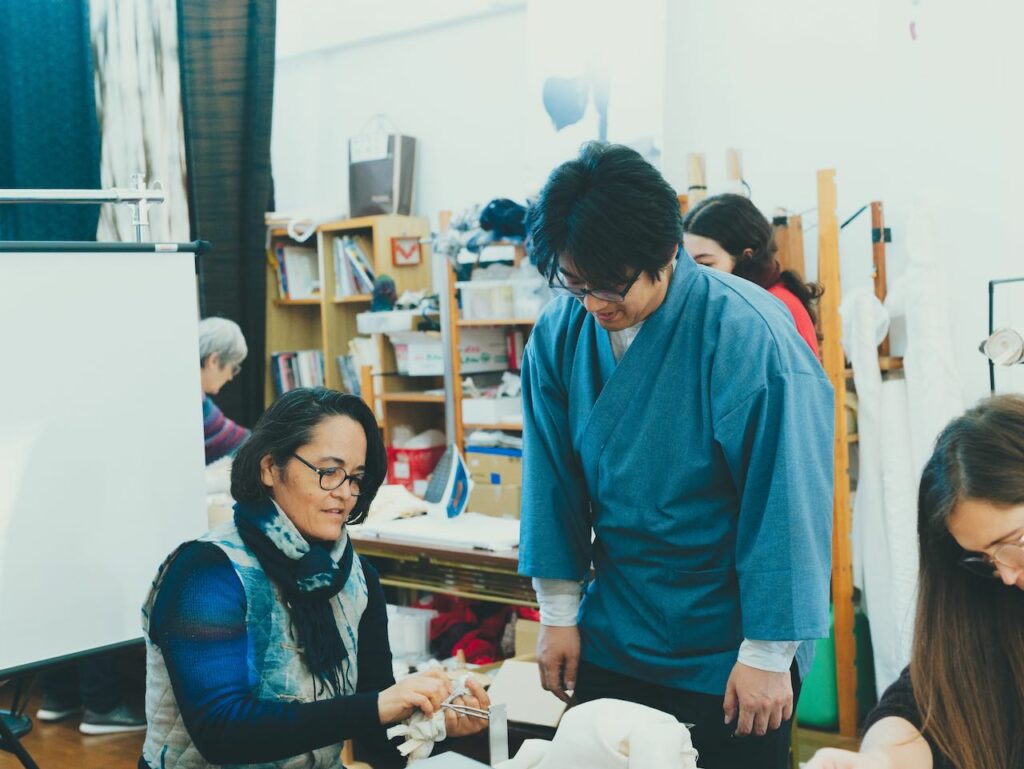
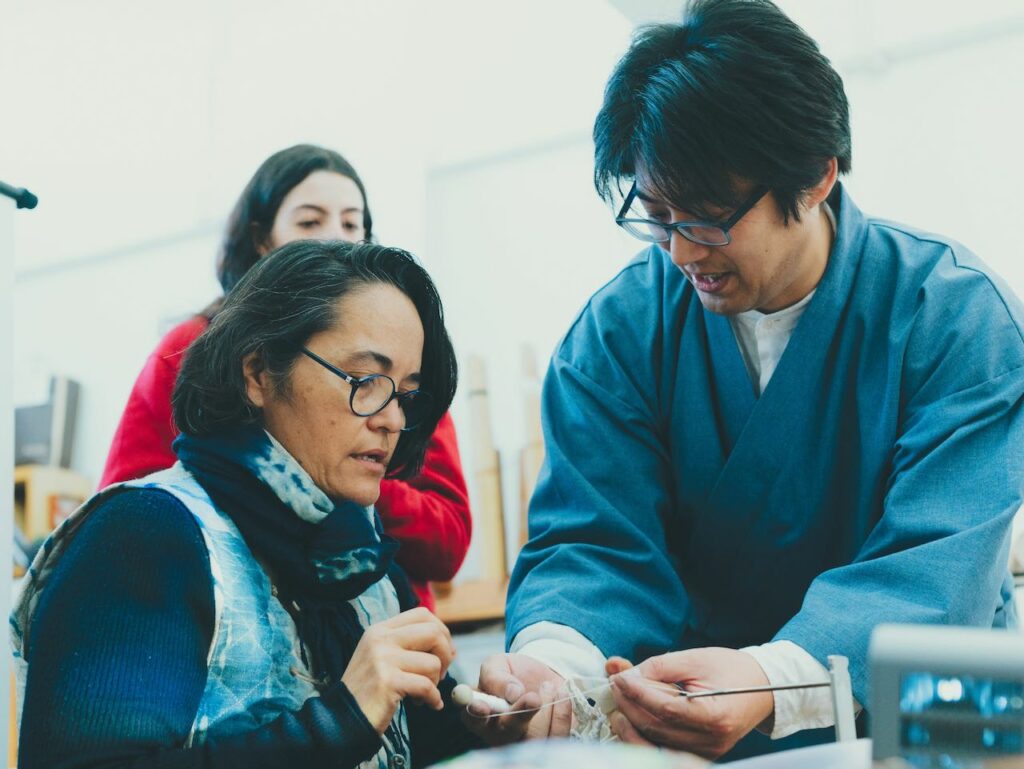
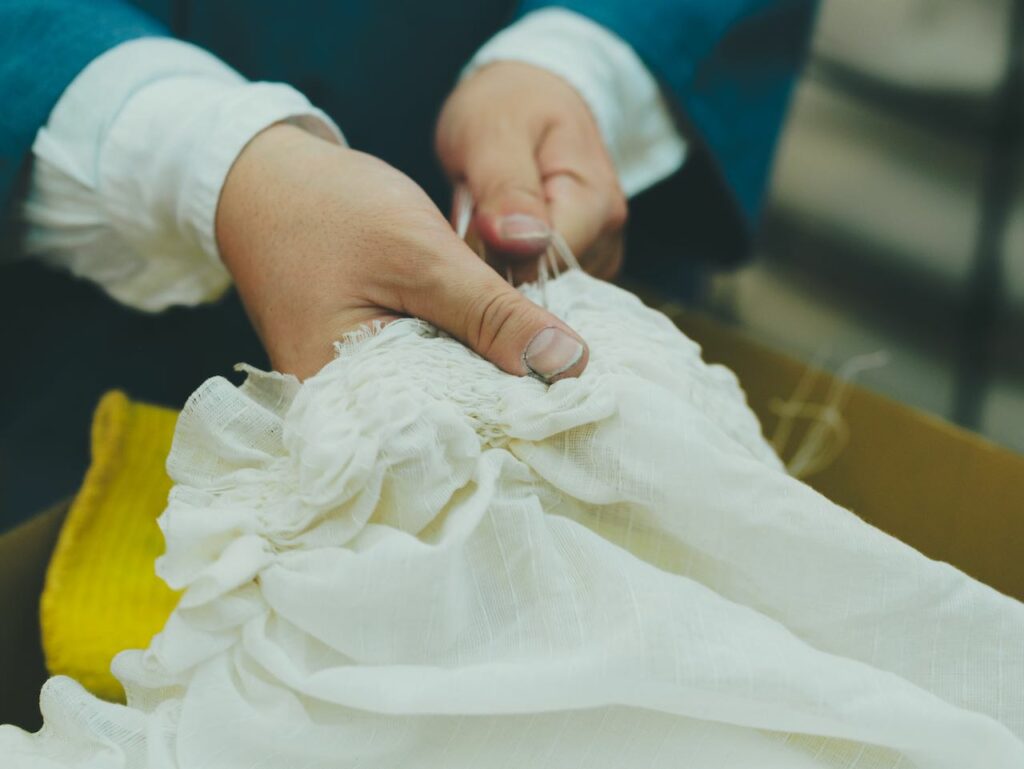
Last steps where indigo dyeing and once rinsed and dried, the fixing of the 3d shape in Kunosan’s atelier. Bellow some testing of Mokume, Makiage, Karamatsu, Bouzishibori, gangimokume shiboris, fater dyeing and 3d fixing.
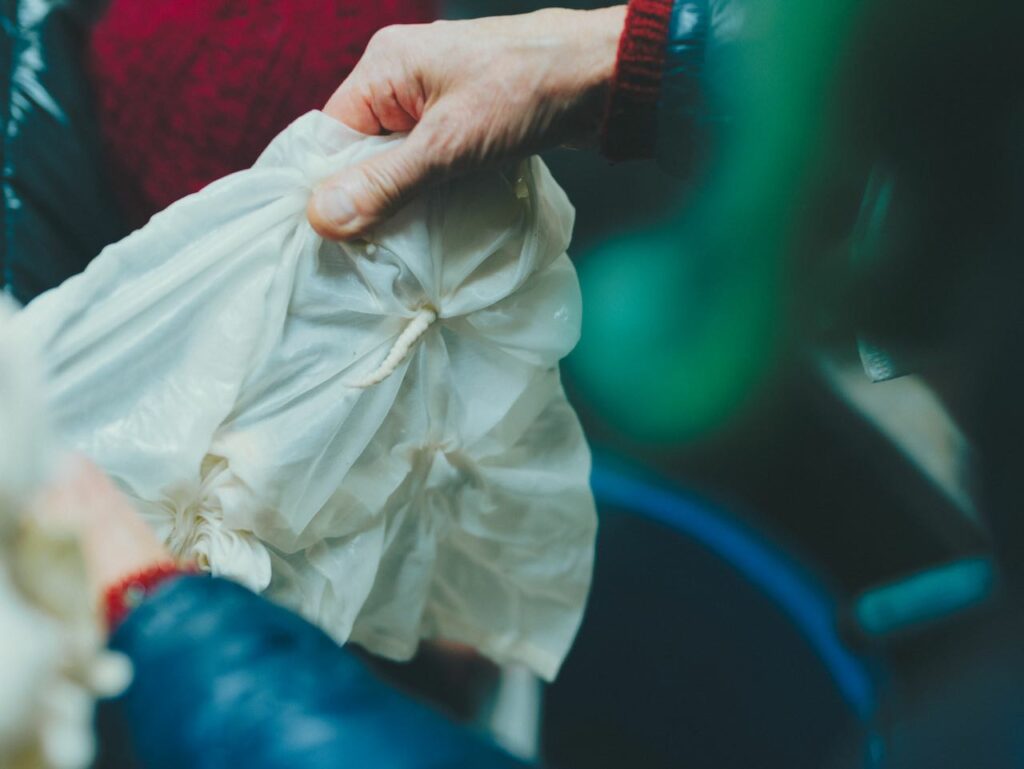
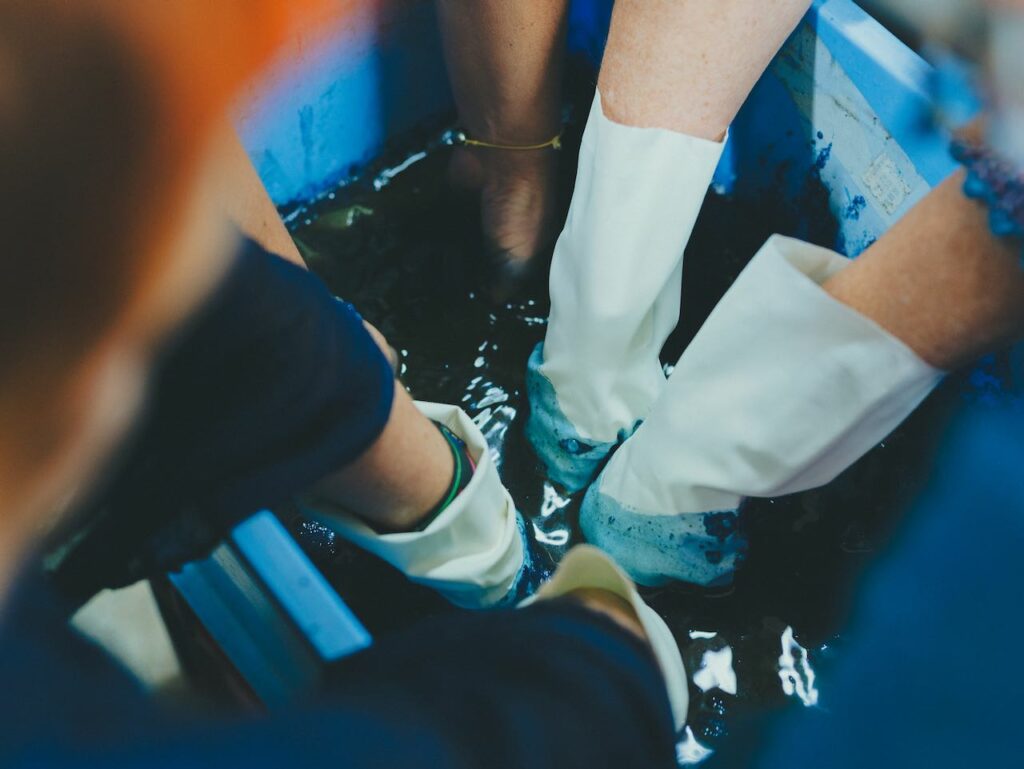
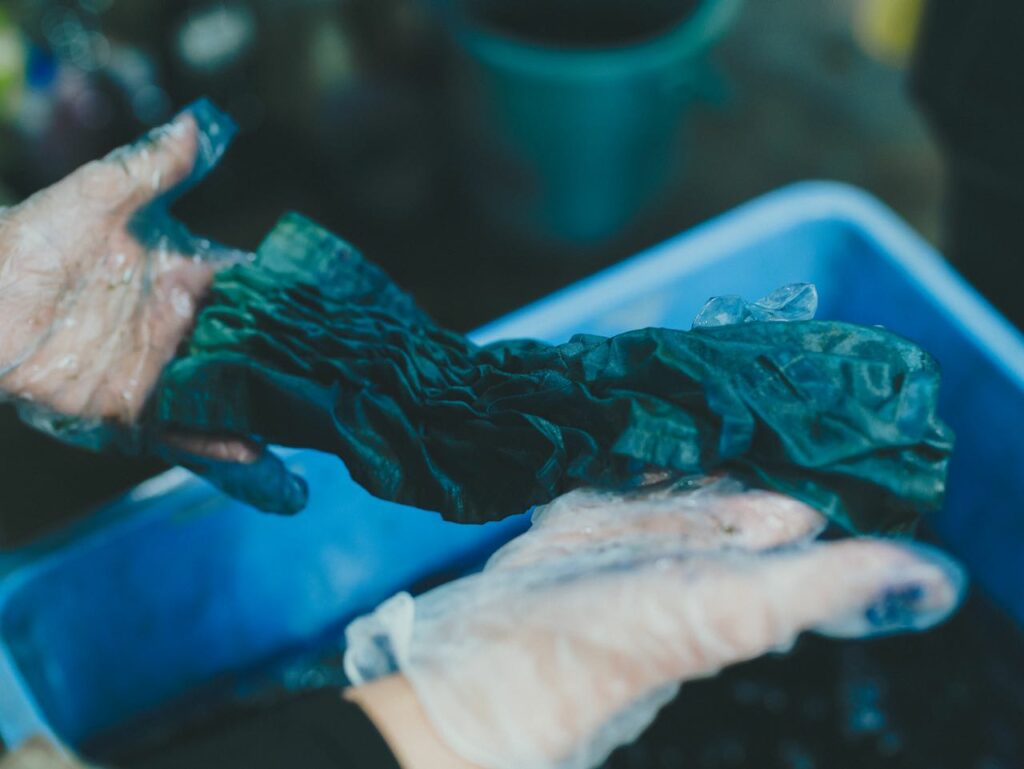
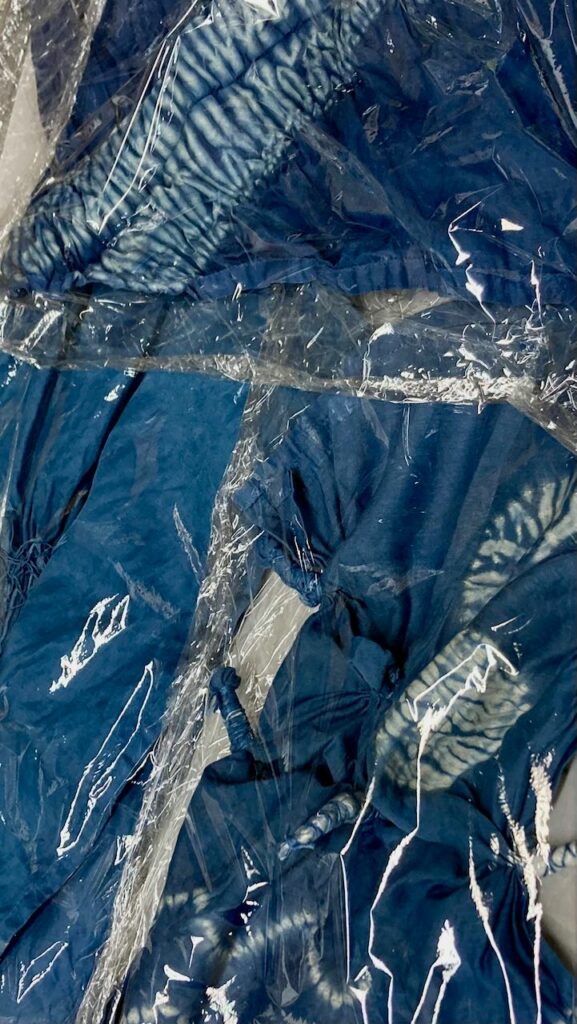
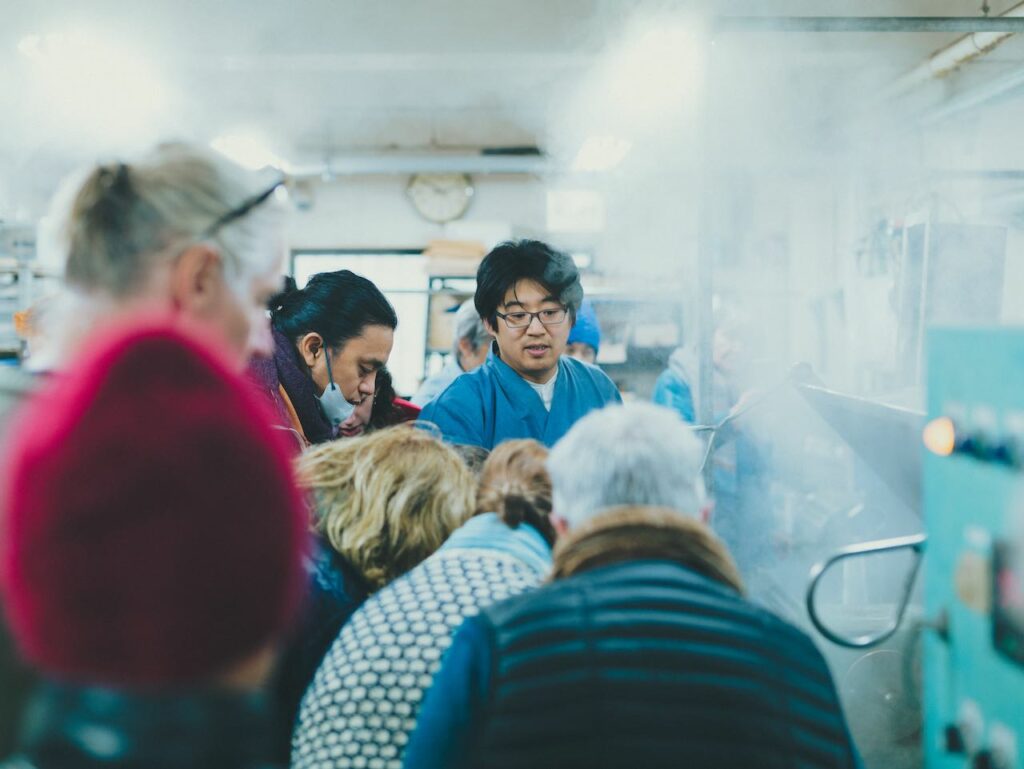
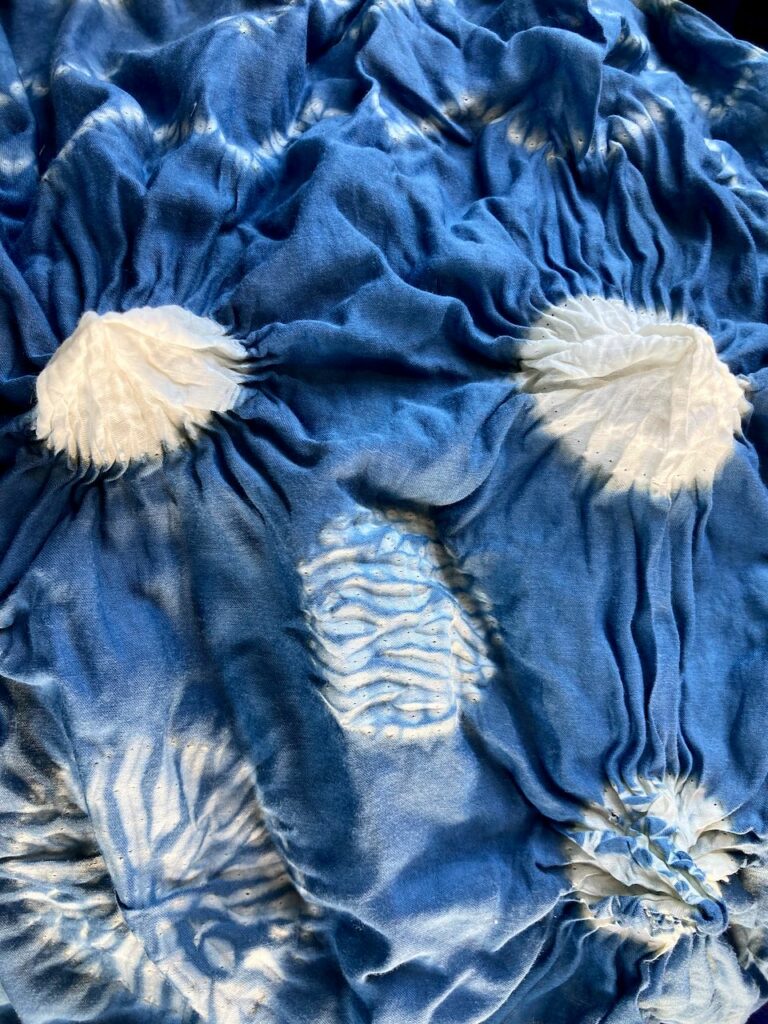
And to finish off, some shots from the Shibori Museum in Arimatsu, showcasing the precious work of life long artisans. They come to show how long the road is to master those exacting techniques.
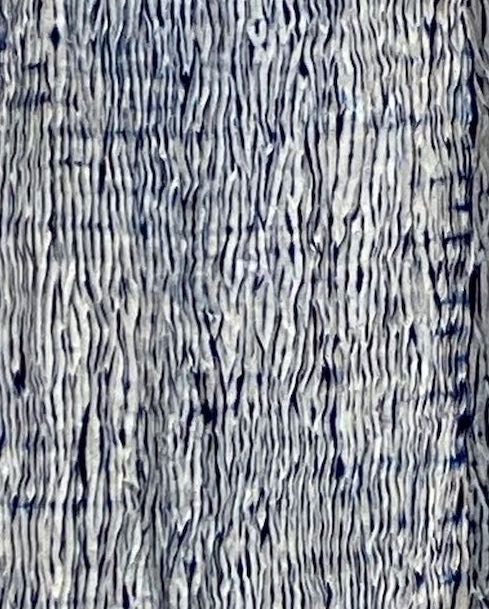
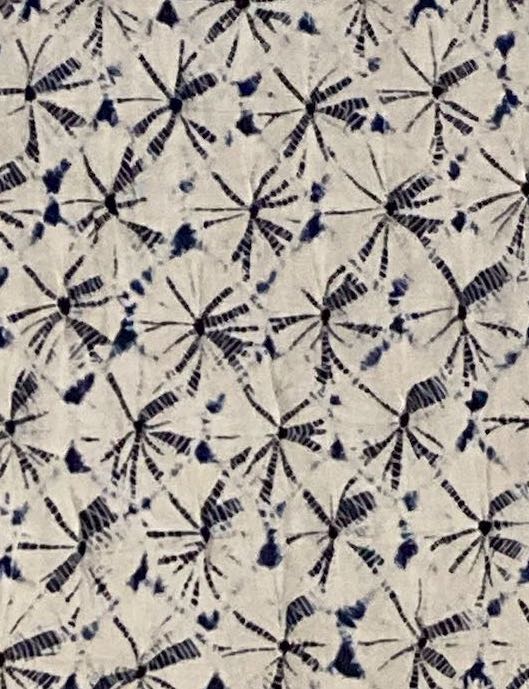
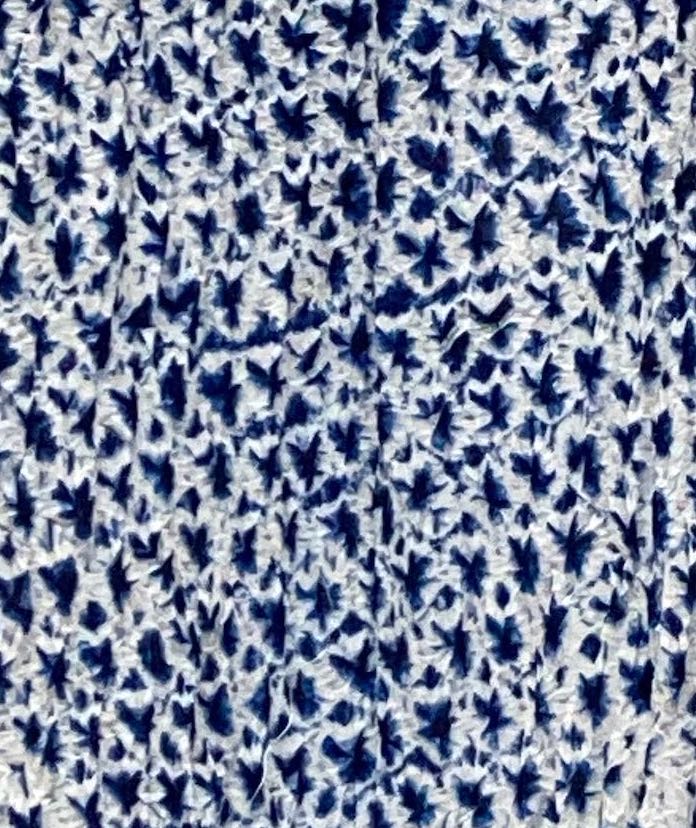
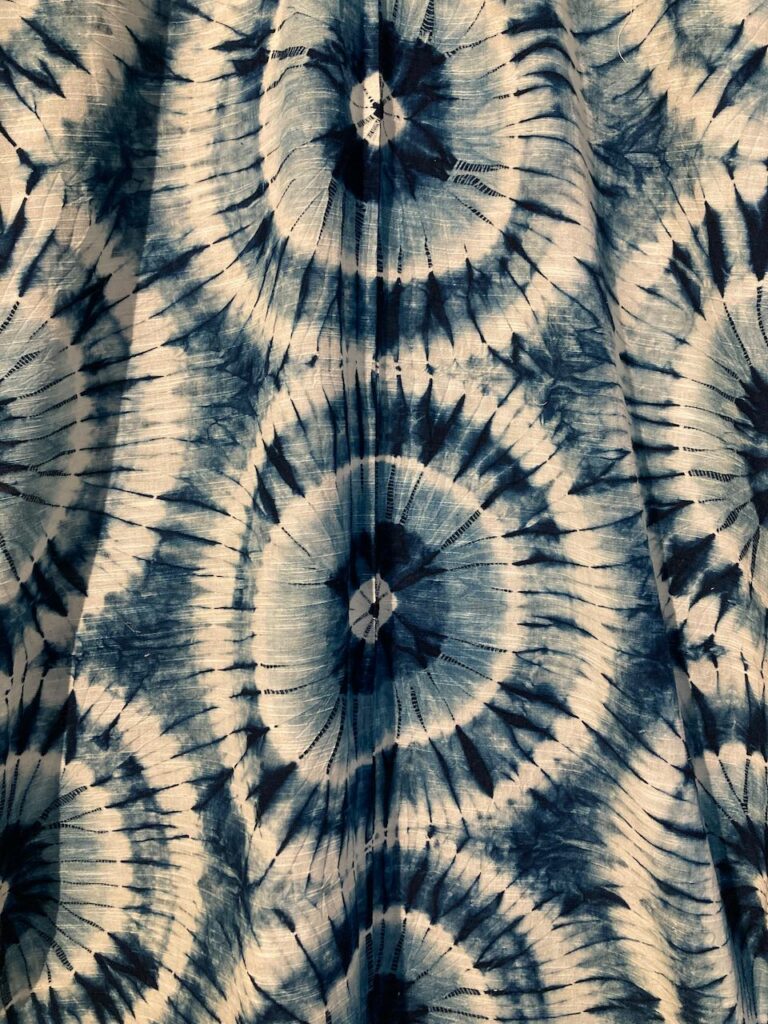
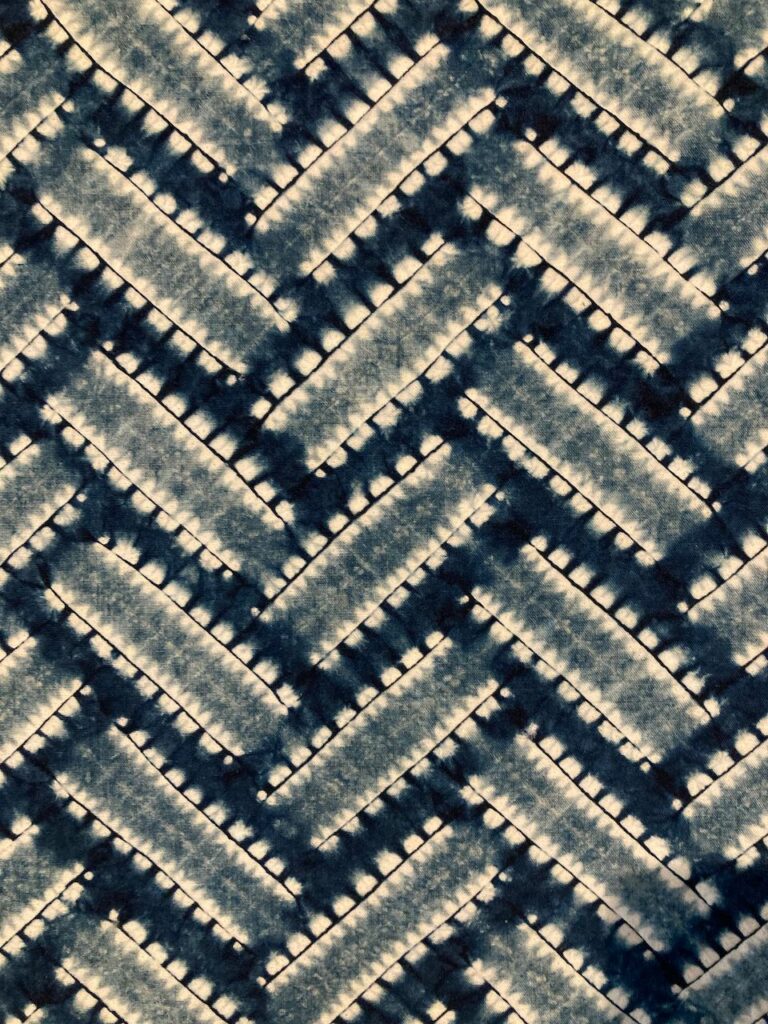
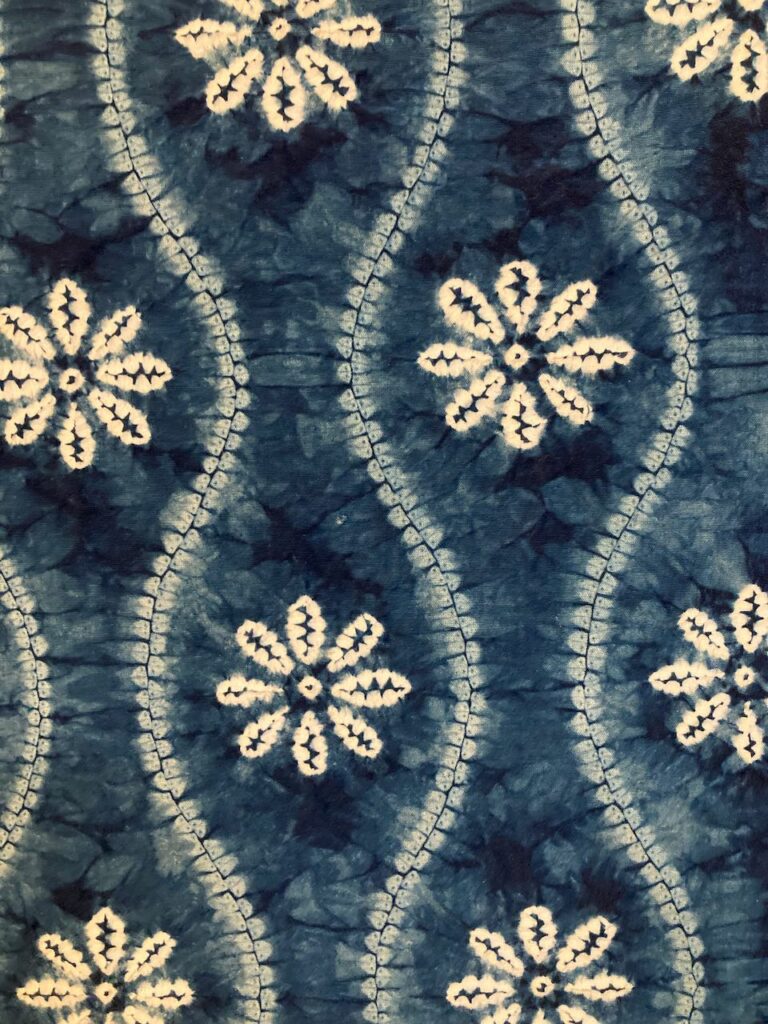
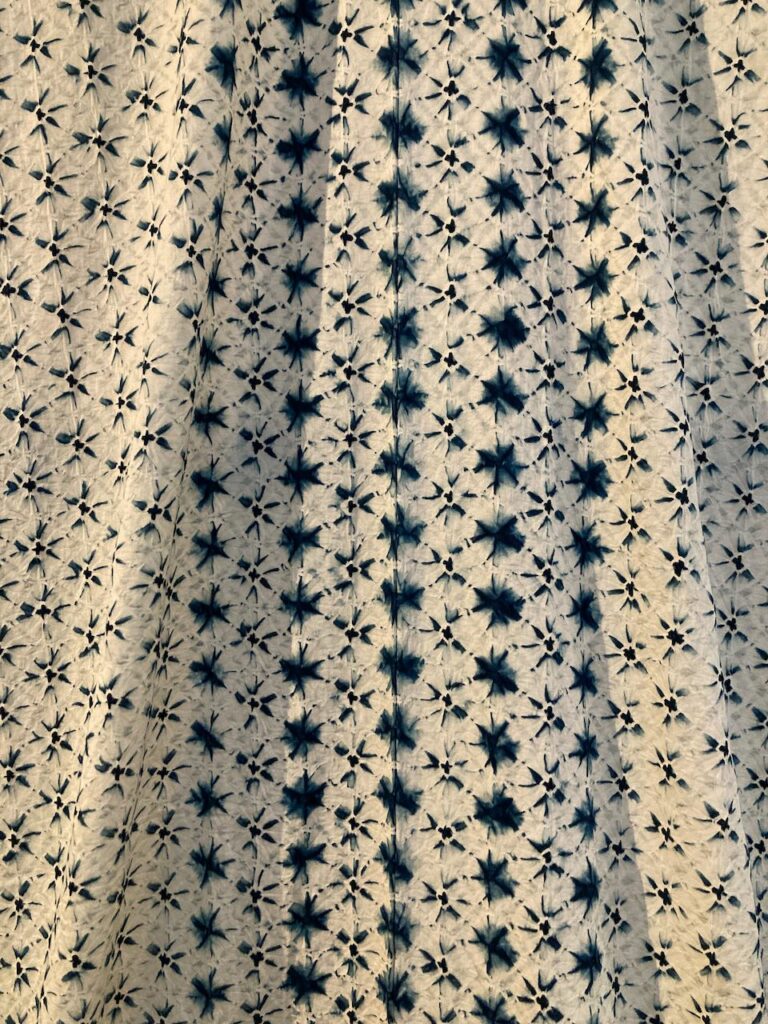
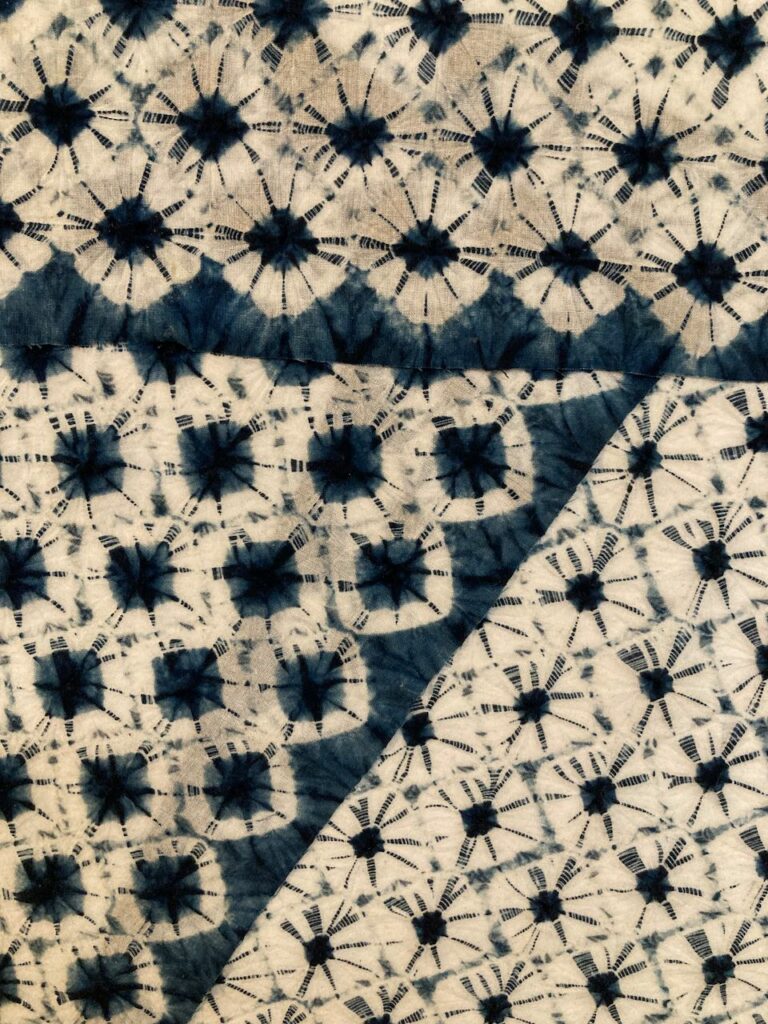
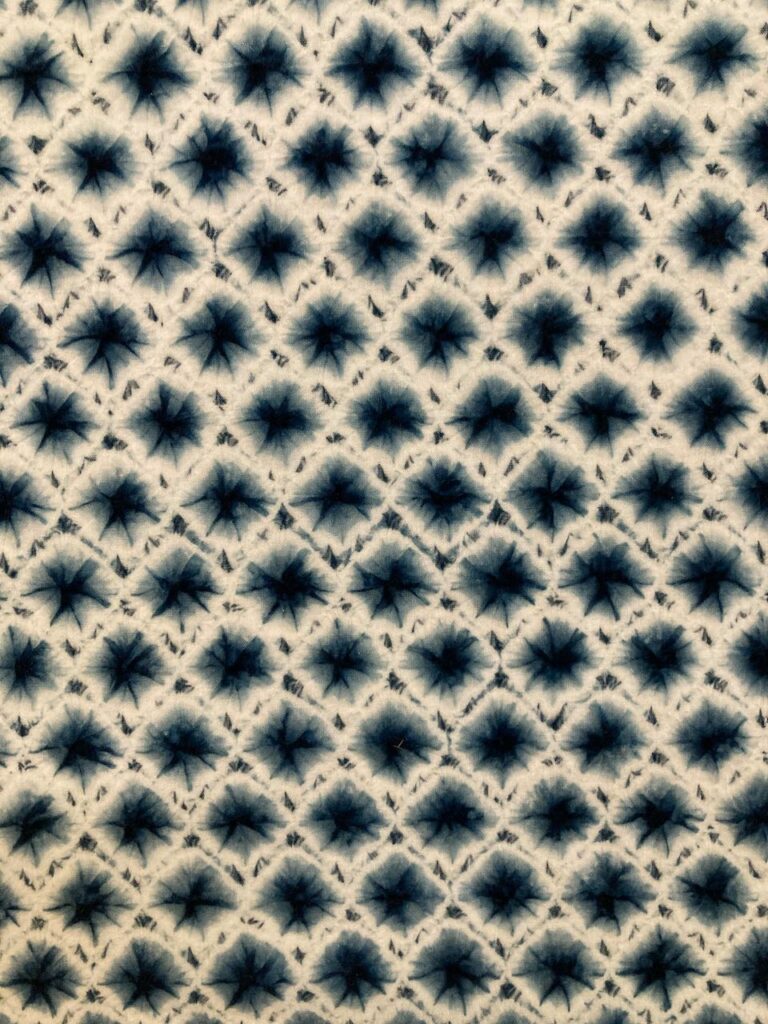
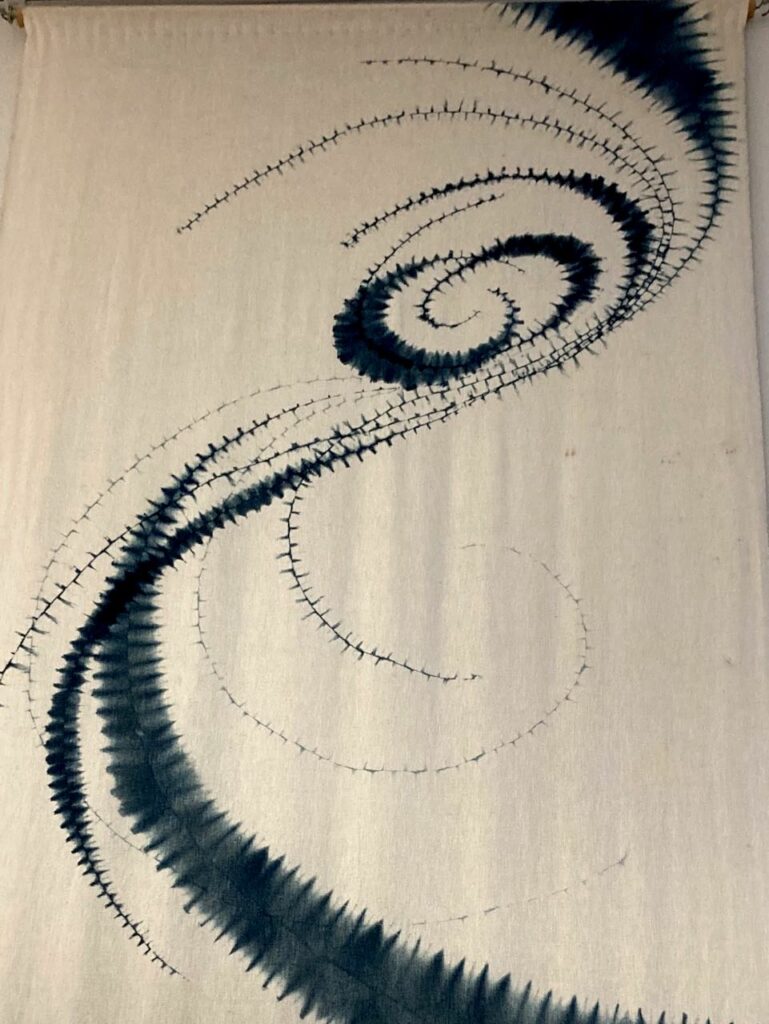
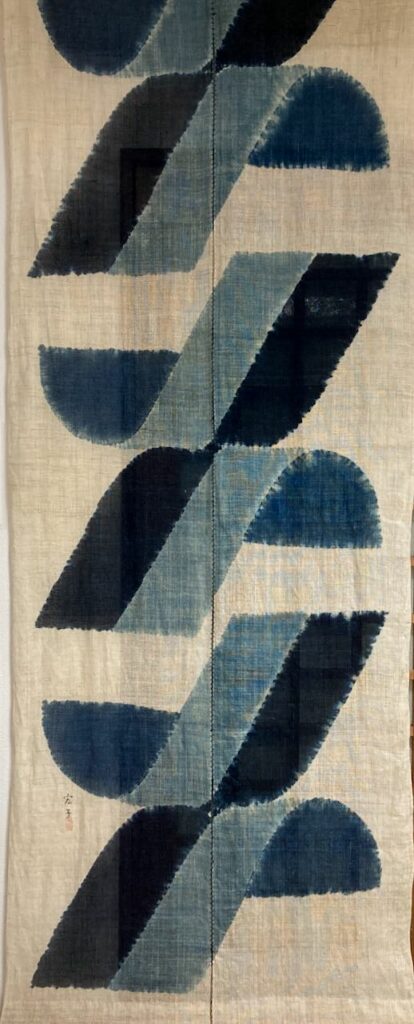
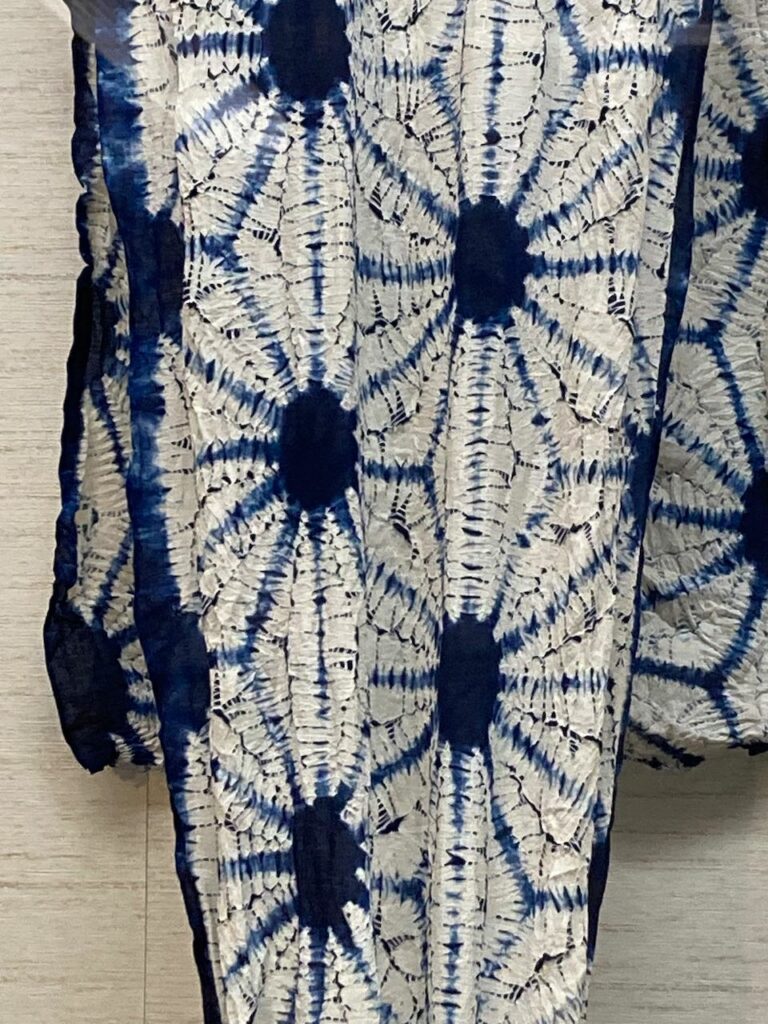